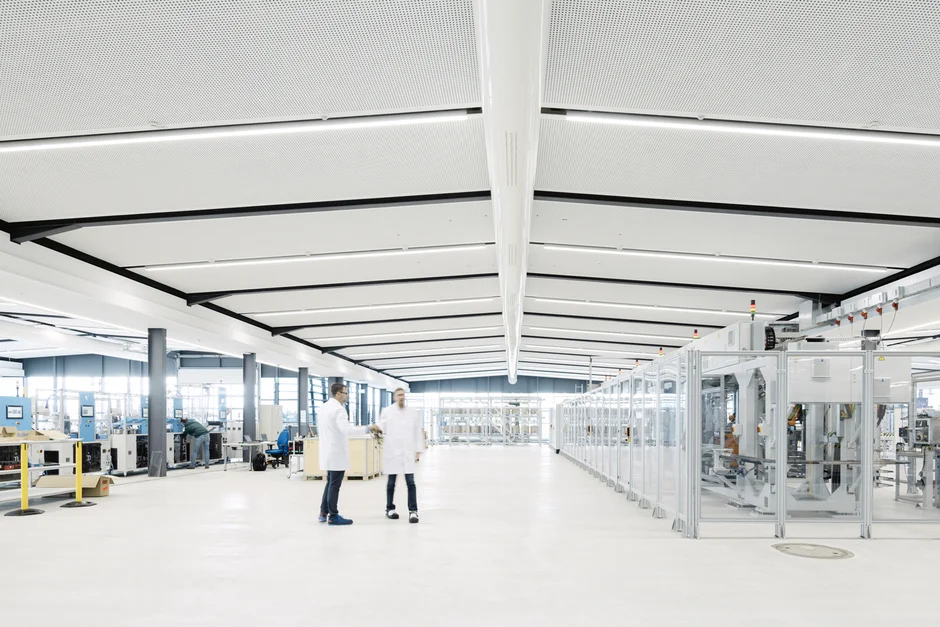
Innovation Industrialization Center
Think tank for tomorrow's mobility
Since September 2022, LEONI unites expertise for maximum innovation, efficiency and pioneering production/manufacturing approaches in our Innovation Industrialization Center (iiC) in Kitzingen. This think tank houses laboratories, offices and a generous open space over an area of 3,000 square meters, where developers, production specialists and international experts come together. The consolidated know-how is used to standardize processes that are then rolled out to plants worldwide, ultimately leading to greater efficiency and shorter time-to-market.
Information
Researchers, engineers and production specialists develop new wiring system architectures for the mobility of tomorrow in the think tank.
In future, we will combine experts from research, development and production from all Leoni locations into project-related teams in an area the size of two and a half Olympic swimming pools.
The globally unique test facility enables the fully automated production of smaller cable harnesses.

Opening in September 2022
Researchers, engineers and production specialists develop new wiring system architectures for the mobility of tomorrow in the think tank.

Area of about 3000qm
In future, we will combine experts from research, development and production from all Leoni locations into project-related teams in an area the size of two and a half Olympic swimming pools.

Around 14 ongoing projects
The globally unique test facility enables the fully automated production of smaller cable harnesses.
Projects at the iiC
Innovation as well as optimization of processes - as a think tank or incubator, we at the iiC work on things until they are perfect, thus saving us time in the plants. Automation is playing an increasingly important role in this. Here you can find an overview of some current projects.
Fabian Dietlein
Team Leader Process Automation Digitalization