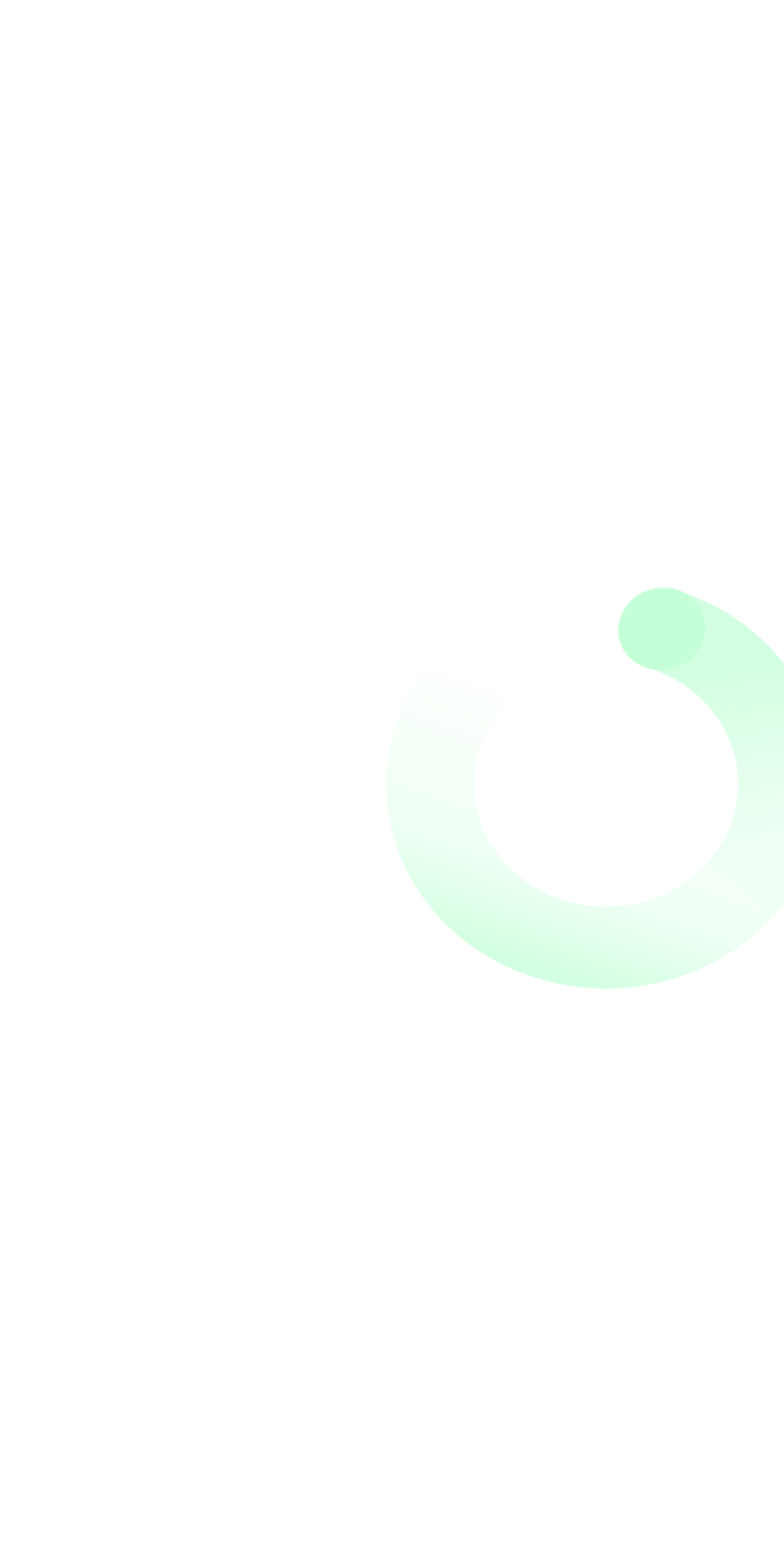
Sustainovation
On the way to a more sustainable future
Sustainability has become one of the most visible topics in the automotive industry. This is due to a variety of factors: the complexity of vehicles and their supply chains, the diversity of resources needed as well as regulatory and social requirements. In addition, mobility is one of the central needs in every society. In view of all these aspects, it is clear what a major influence the automotive industry has on the world – entailing the accountability for sensible and conscious resource usage.
We consider this responsibility from the very beginning of the product design: LEONI only defines an innovation as such, if it brings with it a sustainability advantage. This benefit must be recognizable in at least one of the two dimensions – social and ecological – without jeopardizing the other. This means, for instance, that bio-based materials need to be made out of resources that grow areas which are not suitable for foodstuff production.
New paths through the circular economy
As our customers evolve from car manufacturers to mobility providers, we are transforming our products and our portfolio together with them. For us, the circular economy is an important driver of technological innovation. Circular business models require new approaches in engineering, product development, quality management, sales and customer service. Our starting point is the pre-development – this is where we investigate new design rules and introduce new solutions for dismantling wire harnesses. We are striving to keep materials in the automotive cycle for longer without downcycling and are working with customers on such use cases. While an average of 40% of copper and 76% of aluminum is already recycled worldwide, plastics, for example in insulations and harness-attached parts, pose greater circularity challenges. This is because mechanically recycled plastics can lose some properties, so their use in the same application is limited to a certain number of cycles.
This is why we are actively engaging with established and new partners in our supply chain for selecting the optimal material considering all customer requirements. Wherever technically possible and economically viable, we replace primary materials with secondary ones. We hereby take into account technical specifications and further customer needs regarding the quality, stability and availability of recycled materials.
Our Sustainovation approach
5 workflows to reducing the carbon footprint of our products, which are integrated into our development projects.

Recycled materials for add-on parts and, in the longer term, for wire insulation

Bio-based materials for insulation and add-on parts

Usage of aluminium for busbars and wires to support light-weighting

Weight reduction of plastic parts

Consideration of the principles of the circular economy in the design.
CO2 footprint as a decision criterion in the design process
Through our activities, we are helping to shape the transformation towards a climate-aware economy. On the one hand, we are tackling supply chain transparency with our partners. On the other hand, we are introducing the carbon footprint as a decision-making criterion in our product development processes. This influences design decisions, for example with regard to the types of polymers. In addition, we are driving the wider introduction of aluminum in the wire harnesses, which brings a weight advantage of around 40%. With regard to busbars and electromechanical parts such as fuse and relay boxes, we provide concepts for better dismantlability. Further, we deliver on our green design rules, inspire current suppliers and involve remarkable new ones, while technologically focusing on the shift to zonal architectures. In doing so, our aim is to be the first choice of customers looking for a wiring harness with a low carbon footprint.