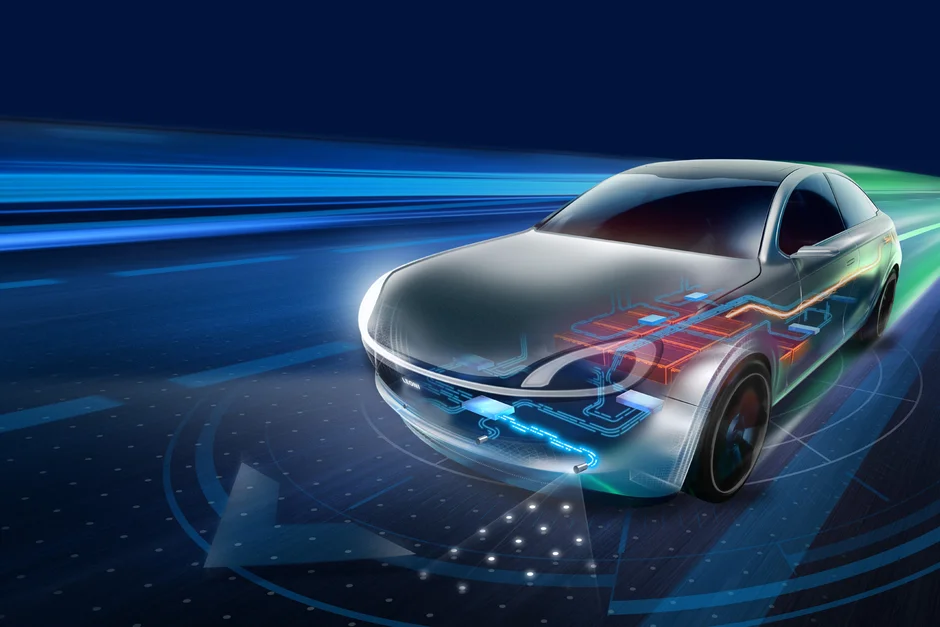
Zonal Architecture
Harness the full potential of wiring systems
Future trends in the automotive industry such as autonomous driving and connectivity bring new requirements with them and present wiring system manufacturers with additional challenges. With more than 100 control units and 1000 individual cables, the current customer-specific wiring system is already reaching the limits of what can still be managed in both production and final assembly. The wiring system needs to be rethought. The solution is zonal architecture.
Zonal Architecture as an enabler
The zonal architecture divides the monolithic wiring system into several sub-harnesses, which reduces complexity in development and production. A few high-performance computers act as local intelligence, managing the distribution of energy and data. This type of architecture also enables the standardization of processes, components and interfaces as well as the (partially) automated production of sub-wiring systems - initially for smaller harnesses, but in future also for larger harnesses.
The zonal approach enables the degree of automation in wire harness production to be increased to well over 50% and simplifies handling in logistics. The resulting reduction in labor costs would therefore open up new opportunities for locations close to the OEM assembly plants. This strengthens the resilience of sourcing and supply chains.
The smaller the sub-harness, the easier it is to install in the vehicle and therefore makes a significant contribution to reducing production times per vehicle. These new configuration options in vehicle assembly as well as a higher level of standardization and scalability create noticeable cost benefits at an overall level.
LEONI estimates that the weight of a comprehensively optimized zone architecture could be reduced by 20 to 30 % compared to today's customer-specific cable harnesses. In combination with a higher geographical proximity of harness production, there is enormous potential for a smaller ecological footprint.

New supply chain and production opportunities
The zonal approach enables the degree of automation in wire harness production to be increased to well over 50% and simplifies handling in logistics. The resulting reduction in labor costs would therefore open up new opportunities for locations close to the OEM assembly plants. This strengthens the resilience of sourcing and supply chains.

Lower total cost of ownership
The smaller the sub-harness, the easier it is to install in the vehicle and therefore makes a significant contribution to reducing production times per vehicle. These new configuration options in vehicle assembly as well as a higher level of standardization and scalability create noticeable cost benefits at an overall level.

Driving sustainability
LEONI estimates that the weight of a comprehensively optimized zone architecture could be reduced by 20 to 30 % compared to today's customer-specific cable harnesses. In combination with a higher geographical proximity of harness production, there is enormous potential for a smaller ecological footprint.
Evolution steps
Even though smaller cable harnesses have long been the focus of wiring system manufacturers and OEMs, it is foreseeable that the change to zonal architecture will not be disruptive, but a smooth transition. LEONI divides this technological change into three phases:
- Phase 1: The foreseeable end of generic further optimization of today's customer-specific cable harnesses.
- Phase 2: The zonal approach 1.0, which is characterized by a multi-domain architecture in combination with some high-performance computers and will gain momentum from 2025. Initial standardizations and simplifications will enable the introduction of highly automated production of certain zones. In this step, busbars can already be used as a central power backbone as well as new solutions for the increased introduction of data networks.
- Phase 3: The zonal approach 2.0, which LEONI believes will become increasingly important from the end of this decade. This scenario could be characterized by an alignment of the functional zones with the OEMs' production modules.
Partner for the wiring system architecture of tomorrow
Thanks to decades of experience in the development and production of complex customer-specific cable harnesses, LEONI has a far-reaching system view of the entire electrical/electronic (E/E) architecture. In addition, we disassemble and examine current production vehicles in our benchmark area in order to identify the latest trends for us and our customers.
With this sound background knowledge, we are already working closely with our customers in joint pre-development projects at the topology level - from the step-by-step definition of the architecture to identifying potential for a higher degree of automation of the production processes through to optimization in terms of functionality, installation space and weight. On the product side, LEONI will increasingly use innovations such as intelligent power distributors to ensure energy supply and voltage stability in the wiring system. By 2026, LEONI – together with its cooperation partner Valeo – will also bring high-performance zone controllers into production.
The company is currently developing busbars as the backbone for power distribution in zonal architectures: In the future, they will supply the central computers and other energy consumers with energy and, as highly functionally integrated units, are already designed for automated production and assembly. In our Innovation Industrialization Center, we also work closely with production experts and colleagues from the plants in the early stages to manufacture the zones in an efficient and automated way.